
PVC Chemicals
PVC Chemicals
PVC chemicals are essential in producing a wide range of products, from pipes and cables to flooring and wall coverings. These chemicals include plasticizers, stabilizers, and fillers that enhance the properties of PVC, making it versatile and durable. By leveraging the benefits of PVC chemicals, manufacturers can create materials that are strong, flexible, and resistant to environmental factors, meeting diverse industry demands.
The role of PVC chemicals in construction cannot be overstated. They ensure that PVC pipes and profiles are robust enough to withstand high pressure and varying temperatures, making them ideal for plumbing and electrical applications. PVC chemicals also contribute to the longevity of these materials, reducing the need for frequent replacements and maintenance. This durability translates to cost savings and increased efficiency for both builders and end-users.
In the realm of consumer goods, PVC chemicals are pivotal in producing items that are both functional and aesthetically pleasing. From synthetic leather to vinyl records, the application of PVC chemicals enhances the quality and appeal of these products. The versatility of PVC chemicals allows for the creation of materials that are not only practical but also customizable in terms of color, texture, and design. This adaptability ensures that PVC remains a preferred choice across various sectors, driven by continuous innovations in PVC chemical formulations.
PVC RESIN
PVC is an acronym for polyvinyl chloride. A resin is a material often used in the production of plastics and rubbers. PVC resin is a white powder commonly used to produce thermoplastics.
Other members of the vinyl family can be used for similar applications, but PVC tends to be the most popular member of that family. It is believed to be superior to other options because it can be produced in numerous forms and used to create a wide array of items for many industries. Products made with PVC resin include blood bags, windows, and pipes.
Production of PVC resin generally relies heavily on the use of chlorine and crude oil. There are four manufacturing processes commonly used in its production. They are the suspension method, the mass method, the emulsion/dispersion method, and the solution method.
PVC resin alone is a raw material. It can be made into products with a wide range of properties from soft and flexible to light and rigid. The outcome is often determined by additives. Other ingredients must typically be added to convert this resin into a finished product. These can include heat stabilizers, lubricants, and fillers. One of the most common types of additives to be blended with PVC is plasticizers, such asbutyl glycolate, epoxy resins, and dialkyl azelates.

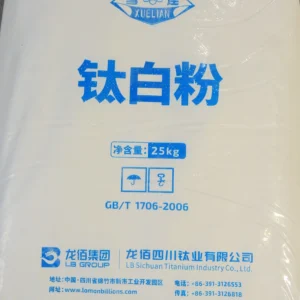
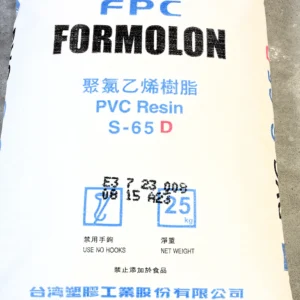
There are many benefits in plasticized PVC. Since it is a thermoplastic, meaning it can be melted down and reformed, PVC is often produced into sheets that will be reworked later. These are normally hard.
When plasticizers are added, the material tends to become much more flexible and pliable than it otherwise would be. The chemical resistance, stress resistance, and puncture resistance can also be increased. PVC in the plasticized form is extremely popular.
PVC resin generally has a high level of chemical resistance. This may not be seen, however, when the material is exposed to organic chemicals. PVC is also strong and resistant to water and abrasion. This material is very popular in the construction industry. It can be used to produce many items needed in the building process. Those items are often lightweight, long lasting and maintenance-free.
One weakness of PVC resin is ultraviolet exposure. The negative effects can often be reduced by additives such as plasticizers. In most cases, however, it is recommended to avoid this type of exposure.
APPLICATIONS
Pipes, conduits and Tubings -(PR 065)
Rigid flexible and corrugated pipes Suction hose and tubings Irrigation systems – (PR 065)
Sewerage and sanitary pipes Electrical conduits – (PR 065)
Fittings & Profiles
Automobiles & Sanitary fittings Doors & window fencing Panelling & railings – (PR 065)
Wires & Cables – (PR 065)
Bottles & Containers (PR 057)
PE WAX
Polyethylene wax is a low molecular weight polyethylene polymer that is used for improving and enhancing the process parameters and properties of the finished products in diverse applications in the plastic industry. PE WAX is very good external lubricant for PVC. When PE Wax use in PVC application, final produce face has been shine. PE Wax using decrease the friction so increase the extrusion capacity.
PE wax has a large variety of uses and applications. PE Wax is available from on-purpose production and as a byproduct of polyethylene production. This material is
available in both HDPE and LDPE forms. As there are many grades and types available, please inquire so that one of our knowledgeable representatives can assist you in locating the correct grade that matches your requirements.
There are a variety of methods for producing Polyethylene wax. Polyethylene wax can be made
by direct polymerization of ethylene under special conditions that control molecular weight. Another method involves breaking down high molecular weight
polyethylene into lower molecular weight fractions. A third method involves separation of the low molecular weight fraction from high molecular weight polymer.
There are three major characteristics that differentiate one PE wax from another. They are I) Molecular weight, II) Degree and length of polymer branching, III) Monomer / polymer composition. Changing any of these factors will alter the physical characteristics of the polyethylene wax, such as viscosity, hardness, melt point, reactivity etc.
Paraffin wax is usually produced as a by-product of oil refining. It has a molecular weight which is usually less than half that of most polyethylene waxes. Because of this and other differences, paraffin wax usually
has a much lower melt point and is softer than most polyethylene waxes.
Polyethylene waxes have very unique polymer properties that make them useful in many applications. The major functions of PE wax in many formulations are to either provide lubrication and/or provide physical modification of a formula by changing viscosity and /or melt point.
-
- Polyethylene wax increase inorganic and organic pigment dispersion in matrix polymer during masterbach processing. Also, PE wax helps granule produce by decrease softening point of system.
-
- Polyethylene wax is very good external lubricant for PVC. When PE wax use in PVC application, final produce face has been shine.
-
- Polyethylene wax using decrease the friction so increase the extrusion capacity.
-
- Polyethylene wax using doesn’t change the product color because PE wax has got good oxidation resistance.
-
- Polyethylene wax doesn’t bad effect product’s heat and light stability because pe wax doesn’t include catalyzers remnant.
-
- Polyethylene wax increase last product’s light stability.
-
- Polyethylene wax hasn’t got toxic materials so PE wax can be use food packaging applications.
-
- Polyethylene wax use hot melt application.
PVC STABILISERS
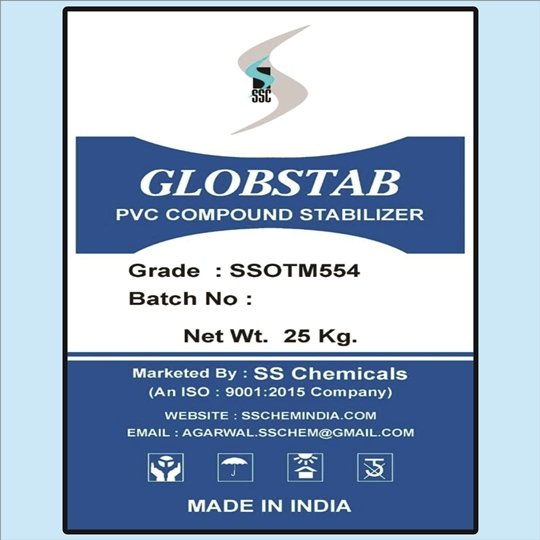
PVC Stabilisers are added either directly into PVC or in combination to prevent oxidation, chain scission, uncontrolled recombination, and cross-linking reactions caused by photo oxidation. Essentially, they protect PVC from the harmful effects of extreme temperature and ultraviolet radiations. PVC Stabilisers are of different types like Heat Stabilisers which are mainly used in Construction projects. Antioxidants are PVC Stabilisers that prevent oxidation of PVC from taking place due to atmospheric oxygen. Hindered amine light stabilizers are PVC Stabilizers that scavenge radicals produced by weathering. The next type of PVC Stabilisers are UV absorbers. They dissipate energy absorbed by UV rays. Antiozonants are PVC Stabilisers that prevent degradation of materials cause by Ozone gas present in the atmosphere. Lastly, PVC Stabilisers are available in the form of Organosulfur Compounds that thermally stabilize polymers.
Usage
PVC Stabilisers are mainly used in the manufacture of Pipes and Fittings, Window Profiles, Rigid and semi-rigid films, wires and cables, coatings, and flooring etc. PVC Stabilisers are available in the form of Heat and UV Stabilisers, Flame Retardants, Smoke Suppressants, Plasticizers, Processing Aids, Impact Modifiers, Thermal Modifiers, Pigments, and Fillers that are added to PVC for strengthening purposes. The applications of a PVC Stabiliser are in all places where PVC is used. PVC is widely used in construction material, medical devices, children’s toys, protective housing for cables and wires, manufacture of credit cards etc. PVC is also used in rubber seals, vinyl fabrics, and automotive parts. Impact Modifier/Processing Aid PVC Stabilisers provide softness and flexibility that PVC does not normally have.
STEARIC ACID
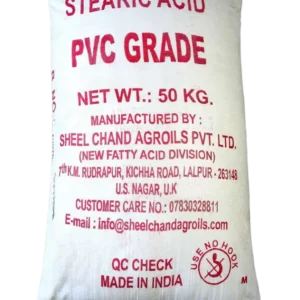
STEARIC ACID is widely used in the manufacture of PVC plastic pipes, sheets, profiles, and films. It is a PVC heat stabilizer with excellent lubricity and good light and heat stability. In plastic PVC pipe, stearic acid helps to prevent “coking” during processing. It is an effective heat stabilizer in the processing of PVC film, and it can prevent the finished film caused by exposure to sulfide discoloration.
What Makes Stearic Acid Suitable for PVC processing?
Thermal Stability
Thermal stability is an essential characteristic of PVC, defining the final product’s thermal degradation. Thermal degradation affects the physical and mechanical properties of the PVC. Besides, it also limits the circularity and the recyclability of PVC pipes and other products. For this reason, companies in PVC processing use thermal stabilizers that hinder labile chlorines, replacing them with solid functional groups that can withstand elimination.
To effectively perform this function, a thermal stabilizer has to be compatible with the PVC. Besides, it must be added in a condition that reduces diffusion time without thermal degradation. The salts and esters of stearic acid are used as thermal stabilizers in PVC and polymer processing.
Uses of Calcium Stearate in PVC
The reaction of stearic acid and lime forms calcium stearate, which acts as an internal lubricant in PVC processing. The white, silky and fine powder is used to reduce the friction in PVC grains, making it a suitable internal lubricant. Compared to wax, calcium stearate has a higher softening point and does not get greasy when exposed to high temperatures. Calcium stearate is also used as a releasing agent and an acid scavenger in the PVC processing industry.